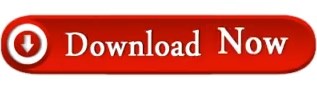
T/3 for T greater than or equal to 19 mm (3/4 in.) and less than or equal to 57 mm (2-1/4 in.) i.e.Any other elongated indication shall be considered unacceptable, which has a length greater than Any crack, lack of penetration, and lack of fusion shall not be acceptedĢ. Acceptance criteria for Linear Indication (UW – 51):ġ. Rounded indications may appear on radiographs from any imperfection in the weld, such as porosity, slag, or tungsten. While determining the size of an indication, the tail shall also be included. A rounded indication may be circular, elliptical, conical, or irregular in shape and may have tails too. Rounded Indication: Any indication with a length equal to or less than three times the width. Linear indications are mainly cracks, lack of penetration, lack of fusion, and elongated slag inclusions. Linear Indication: Any indication with a length greater than three times the width. (Refer: UW-51: Sub Para b ( and 149) and Mandatory Appendix 4 ( and ) of ASME BPVC Section VIII Edition.)įollowing terminologies have been used to explain the acceptance/rejection criteria for Radiography Test (RT) The reduction in thickness shall not exceed 1mm (1/32 in.) or 10% of material nominal thickness whichever is less, provided that the material of the adjoining surfaces below the design thickness at any point.įor the allowable limit of Weld Reinforcement (excess weld metal), Refer to UW-35 (sub-para d, Page – 144).(3 mm).įor an acceptable limit of thickness reduction, Refer to UW-35 (sub-para b, page – 144) which states that: For all other material, the scratch depth shall not exceed 1/8 in. (b) For tubes, the depth of scratch shall not exceed 1/32 in. Cracks in tubes shall not be repaired and shall be considered cause for rejection.
#Astm standards for welding free#
(a) The surface shall be free of any visible laminations, spalling, or cracks. (Refer: UIG-97, Page – 345 of ASME BPVC Section VIII Edition.) (This article covers the weld defect acceptance criteria as per ASME Section VIII Div 1, which is one of the most widely used standards for acceptance criteria for weld defects) Acceptance criteria for Visual Inspection Acceptance criteria for Magnetic Particle Test (MPI/MPT/MT) Acceptance criteria for Liquid Penetrant Test (LPT/LPI/DPT) 5. Acceptance criteria for Ultrasonic Test (UT) 4. Acceptance criteria for Radiography Test (RT) 3. Acceptance criteria for Visual Inspection 2.
#Astm standards for welding iso#
“Static Design Procedure for Welded Hollow-Section Joints – Recommendations”, ISO 14346:2013(E), International Standards Organisation, Geneva, Switzerland.įig.In this article, the weld defect acceptance/rejection criteria are given for the following tests/NDT 1. “Standard Specification for Cold-Formed Welded and Seamless Carbon Steel Structural Tubing in Rounds and Shapes”, ASTM A500/A500M–13, ASTM International, West Conshohocken, PA. This confirms that there are precautions necessary when welding in regions of high cold-forming.ĪSTM, 2013. This standard even states that the distance between the longitudinal seam and the tangent point to the flat should be at least two times the HSS wall thickness, as shown in Fig. not “normative” or mandatory) “Annex A: Quality requirements for hollow sections” which advises against longitudinal seam welds in the corner regions of square and rectangular HSS made by cold-forming. It is worth noting that a recent international standard for HSS welded connections, ISO 14346 (ISO, 2013), also contains an informative (i.e. Thus, a weld seam located beyond the tangent point of an HSS “flat” is cause for rejection of ASTM A500 material, but not ASTM A1085 material at present.
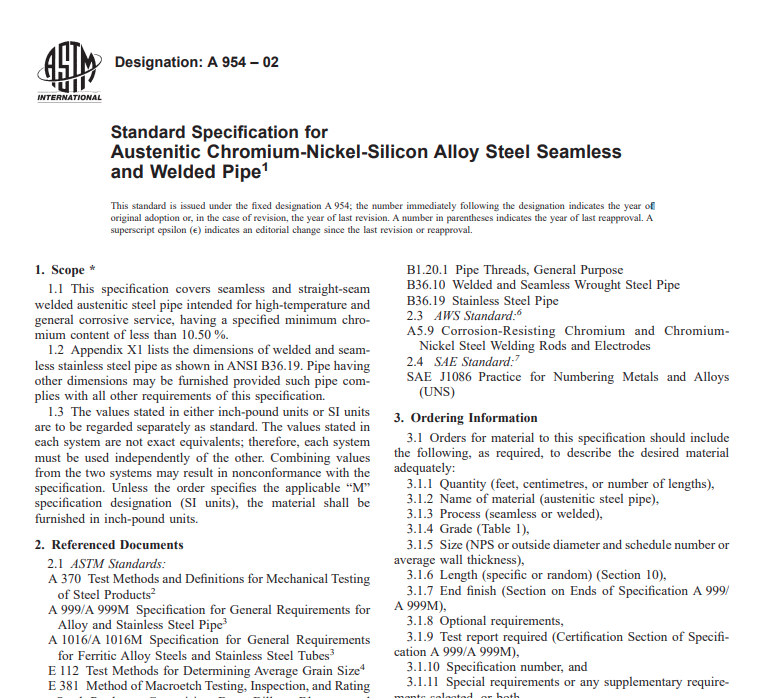
In ASTM A1085-13, however, this prohibition of the seam weld in the corner is not included – yet. There is a lack of experience and testing to support the approval of corner seam welds in regions of high cold-forming, for any structural application, so this “best practice” condition was added to A500. It is generally accepted by HSS manufacturers that longitudinal seam welds should not lie in the corner regions of square and rectangular HSS. (ii) Clause 6.3: A new requirement for the HSS weld seam was added … “The weld shall not be located within the radius of the corners of any shaped tube unless specified by the purchaser”. Thus, the open-hearth process was removed, reflecting current practice. (i) Clause 5.1: The permitted processes to produce the steel were reduced to basic-oxygen and electric-furnace. In 2013, however, an updated edition of the familiar ASTM A500 specification was also released (ASTM A500/A500M–13).

Details of the features of this HSS are readily available: Most users of HSS are now aware of the new ASTM A1085 specification for “higher performance” HSS that was approved in 2013 and immediately manufactured by Atlas Tube.
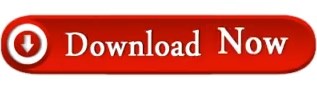